The Janos Interview (part 2)
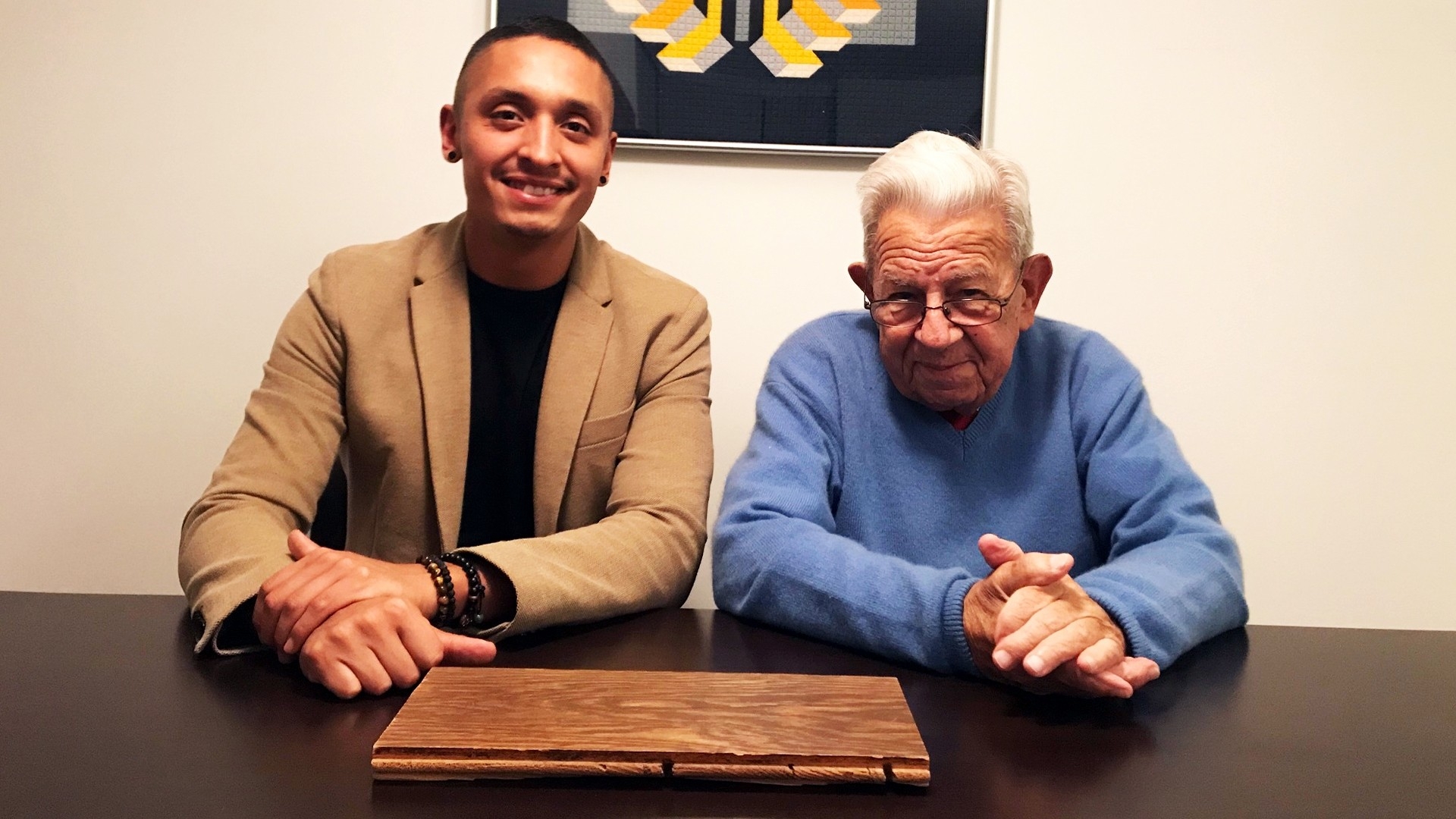
Tuesday, 25 February 2020
With so many years of experience in the flooring industry, Janos had a lot to share about the appearance of engineered wood and the history of acoustic treatments. In this segment, we will highlight parts of the interview touching these subjects. Like in many industries, the craftsmanship of the past set standards for todays’ manufacturers and there has been a lot of trial and error to achieve success. Janos took us down memory lane to show us the motherboard and share some stumbles of the first attempts of treating acoustics. You will find out that over the years some things just stay the same to get better in engineered woods and that the constant evolution in acoustics treatment will lead to better results through trial and error. The keys to success stay the same, mechanical stability and the right product at the right place to achieve a sound flooring system.
If you ask most people when did engineered wood appear in houses, most will think of the 1990s when its popularity grew. When we asked Janos about engineered wood, he got up and reached for a plank:
“I’ve seen engineered wood that is over one hundred years old this is the motherboard. As a matter of fact, when I found this in a park avenue building, I actually researched it and all the really nice building had engineered floors. The engineered floors were done with hyde glue, you know, horse glue. This is a cross banded engineered floor probably late 1800 early 1900. This is cross banded, top and bottom go in the same direction approximately coefficient. So when this wants to move, the cross band restrains it. My friend started his engineered wood plant based on this. This is about 6 inches, but you know, it cross banded, this is why it’s efficient.”
Cross banded flooring has Janos’ seal of approval for its mechanical stability in a flooring assembly. Until the arrival of the newer versions of engineered wood, this type of application was nailed down. Glues arrived with the newer generation of engineered wood. To this date, cross banded engineered woods are considered a high-end solution for manufacturers and installers.
Even the motherboard has the same shortcoming as all hard flooring surfaces, it cannot supress vertical sound transmission on its own as part of a flooring assembly. Acoustic membranes were introduced to flooring assemblies to act as decoupling agent. With trial and error in the early days, where does New York stand in its quest to reduce noise transmission from the floor down?
At first, cork arrive on the market followed by foam, the latest go to product in New-York has been rubber. What is Janos’ take on this and is there room for new solutions?
“In the 70s, the late 70s foam which did not do much for sound attenuation. When the little parquet blocs became popular, the 6 by 6 miniature blocs were usually installed with a foam back. But the adhesive would eat the foam, or would eat the concrete and vice versa, the concrete would eat the adhesive. This chemical reaction would cause complaints one year after the installation.”
“Cork was always an issue. The appearance of cork is similar between the bulletin board and underlayment cork. But It would disintegrate, it was not a reliable solution. It would be used a lot for double glue down applications for parquet.”
Rubber appeared in New-York 15-20 years ago. It has been a popular solution since. With New-York aiming for a zero carbon foot-print and some of the mechanical challenges of working with rubber, Janos believes needle punch technology would have its place in the market. When comparing some basic aspects of rubber and needle punch material, Janos quotes…
“So much more to gain by getting the material up to the job sites.
Getting rubber to the jobsite is a huge problem. One of my job by mistake, they delivered 10 mm rubber exactly the same length instead of 5mm. I weighed 200 lbs, the crew went berserk. So, I told them that these need to be delivered in sheets.
Rolls are awkward to handle. Sheets can be taken off and installed. They don’t curl up. Especially with 10 mm, you put it down, you roll it, but it can’t reach the wall. The next morning it curls up by the wall, so you need to scrape the concrete and put another piece, so it’s extra work and extra material. You’re not cutting off just an inch or two, it’s 5-6 inch. It adds up and not just the material, it’s time. It adds up, the guys need to cut and get ready.
I even talk to guys in Europe, and they say we’re crazy to work with rubber.”
When comparing rubber solutions and AcoustiTECH textile products, the logistics and physical proprieties speak for themselves.
AcoustiTECH is committed to putting the right product at the right place. Since our interview with Janos, Cristian had toured many architectural firms to offer lunch and learn trainings on acoustics, this has led to product testing and having the AcoustiTECH line being specified for building bylaws.
You are living in a multi-storey building that has soundproofing bylaws? Look up the AcoustiCONDO platform and see which AcoustiTECH products are recommended.