Chris Maskell: The truth about LVT floors
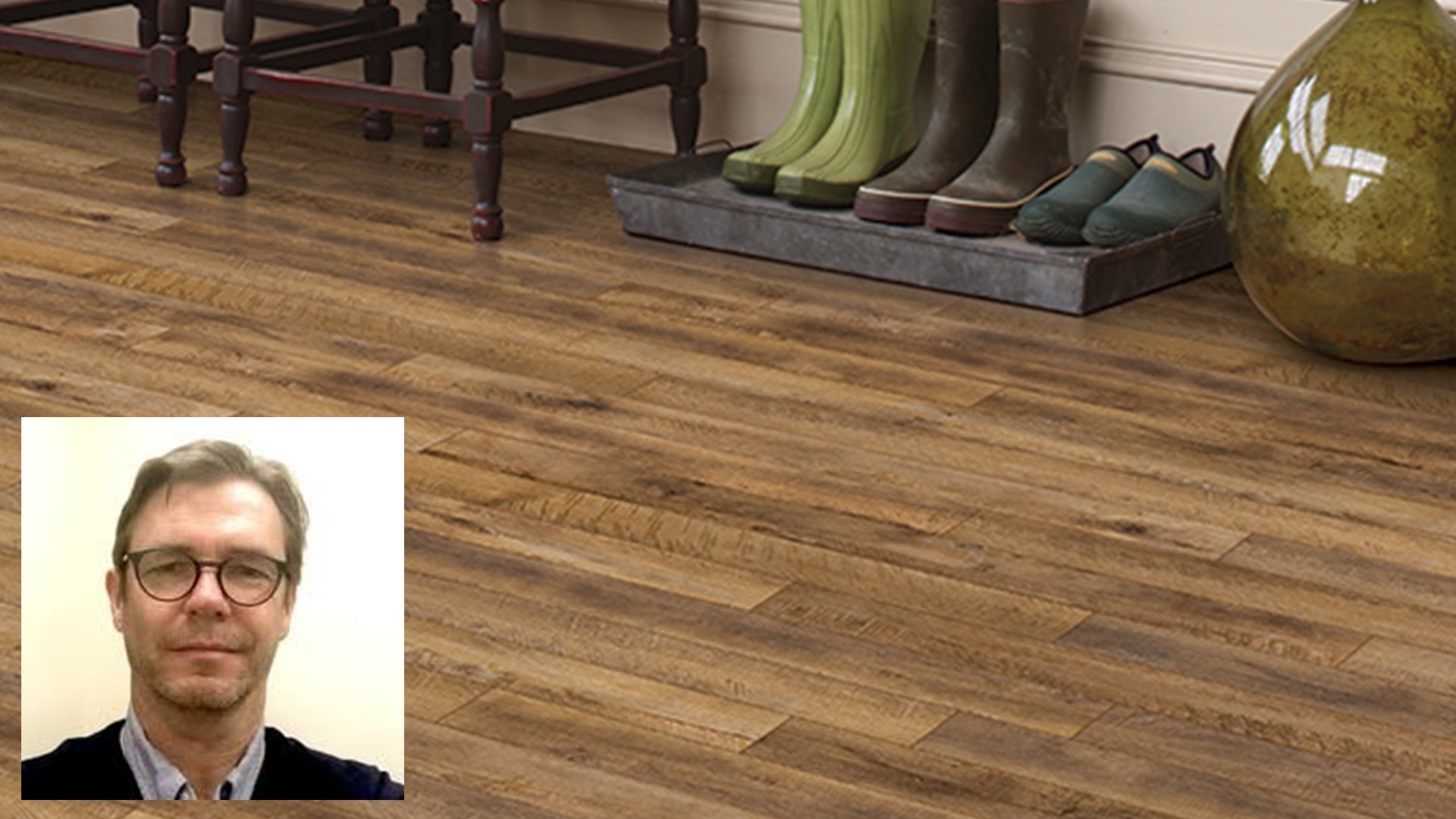
Thursday, 30 May 2019
LVT (Luxury Vinyl Tile) has exploded over the last decade. As a result, it is the cause of a lot of discussion. Everything from great value, fast to install and very durable, to shrinking, buckling and peaking at the seams. Should I glue it down or float a click product? What are the criteria that separate the good from the bad? As usual there's no one silver bullet to answer all the questions. Each client has a different set of needs, set of job site circumstances, time frame and budget influencing the eventual decision. Needless to say, no one wants the problems which seem to be plaguing this sector of the industry.
Our inspectors have seen and reported on many of the problems associated with LVT - problems ranging from using the wrong adhesive to incorrect acclimation, to sunlight overheating the floor, to substrates that are not flat to manufacturer's standards.
I've also had numerous conversations with flooring contractors promoting the benefits of both floating and glue down types of installation, saying they would never install LVT 'the other way' again. I suppose once bitten twice shy. So, here are a few pointers that I hope will help:
- Understand the restrictions for the type of LVT you are installing before delivering the product to site. They are found in the installation guidelines that should come with every carton of material.
- Spend time setting your customers’ expectations regarding what to expect regarding wear and tear and maintenance. Yes, LVT scratches!
- Discuss subfloor flatness and the likelihood that extra work and dollars will be needed to meet the manufacturer's subfloor flatness guidelines. NFCA standards call for 3/16" +/- over 10' feet, 360 degrees.
- Ambient temperature on site should be 18c to 29c. Acclimate the flooring indoors under acceptable conditions for a minimum of 48 hours. Do not deliver material to site conditions that do not meet the manufacturers standards.
- Concrete sub-floor temperature is important. Understand that a concrete substrate can be 10c cooler than the ambient temperature of a room - more than enough to cause significant problems. It is reported that 90% of LVT/P failures occur because the product was installed too cold (here in Canada). Buy an infra-red temperature tester for $50 from Amazon, so you can check product and slab temperature. ‘Log cabin’ the stack of product so that warm air can circulate and bring ALL of the packs up to ideal temperatures.
- When glueing LVT to concrete, moisture and alkalinity levels in the concrete must meet the manufacturer's guidelines. If they don't, then delay the installation, change the product or use a moisture barrier that you know works when high moisture and alkalinity are present.
- For south facing windows, sunlight and heat are the enemy of LVT. Here is a direct quote from the installation guidelines of a well known LVT distributor regarding their product and sunlight/heat effecting the floor.
- Understand why you are choosing either ‘Wet Set’ (transitional) adhesive or ‘Pressure Sensitive’ adhesive. The latter needs a super, clean and smooth surface for a good bond. Wet set needs to transfer 90% of the adhesive to the back of the product and surface. Understand the adhesive products’ specific needs.
- "Avoid exposure to direct sunlight for prolonged periods; such exposure may result in discoloration, and excessive temperatures can cause the flooring to expand and lift off of the sub-floor. During peak sunlight hours, the use of drapes or blinds is recommended."
- Know that it is the flooring contractor's responsibility to check that site conditions meet the manufacturer's recommended levels before shipping the flooring to site. Don't install if conditions are not correct. Installers, protect yourselves by recording these readings prior to installation for future reference should there be a problem. Take a photograph showing the date and a picture of the testing equipment used to record temperature, moisture and relative humidity (RH) levels. Once these conditions are proven to exist and recorded move forward with the installation. If the floor fails because of a moisture issue in 6 months, it won't be deemed the floor installer's fault. At the end of the day it's the home or building owner's responsibility to manage their own building's interior living conditions after installation.
Chris Maskell is the CEO of the NFCA (National Floor Covering Association) since August 2016 in Vancouver (British Columbia). See his LinkedIn profile.